導讀:金屬材料增材制造技術,又稱3D打印技術、激光快速成型技術,由于能夠實現高性能復雜結構金屬零件的無模具、快速、全致密近凈成形,成為應對飛機及航空發動機領域技術挑戰的最佳新技術途徑。

整體葉盤結構示意圖
該技術主要以金屬粉末(尺寸小于1mm的金屬顆粒群)、顆粒或金屬絲材為原料,通過CAD模型預分層處理,采用高功率激光束熔化堆積生長(“增材制造”),直接從CAD模型一步完成高性能構件的“近終成形”。該技術可分為激光選區熔化(SLM)、激光直接沉積(LMD)、電子束選區熔化(SEBM)、電子束熔絲沉積(EBF)和電弧熔絲沉積(WAAM),如圖1所示。
先進飛機的設計、材料與制造技術對于國防工業的發展有關鍵性的作用,先進航空制造技術是體現一個國家科技水平、軍事實力和綜合國力的重要標志之一。為了提高飛機的戰技指標或飛行性能以及經濟性、可靠性,先進飛機和發動機越來越多地增加鈦合金、高溫合金、高強鋁合金和超高強度鋼等高強度合金的用量,且結構越來越復雜,加工精度要求越來越高,對制造工藝提出了更高的要求。此外,通常高強度合金的熱加工和力學性能加工都很困難,飛機及航空發動機中復雜高強度合金構件用量的增加,導致了高強度合金大型復雜整體結構件和精密復雜構件的制造尤為困難,成為制約先進飛機及航空發動機發展的瓶頸之一。
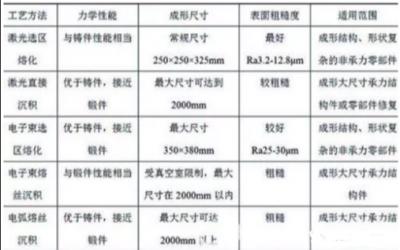
各增材制造技術的特點
結合目前已有的技術成果以及航空發動機零部件的特點,增材制造技術在航空發動機中的應用優勢主要如下:
拓寬設計自由度。航空發動機零部件結構復雜,傳統制造需要模具加工而來。增材制造技術則跨越造模這個環節,無需刀具、模具及工裝卡具,即可將任意復雜形狀的設計方案通過計算機圖形數據快速加工生成實體產品,并能對產品設計進行不斷優化。
減少產品上市時間。通過增材制造技術制造的每件產品都是單獨成形,不需要模具,使復雜的設計不再造成額外成本增加;同時與傳統制造技術相比,增材制造技術通過摒棄生產線而降低成本。從產品的全過程分析,增材制造技術使一些產品零部件的庫存只需要保留電子文檔,而無需制造出來存在倉庫,一旦有需要,直接制造即可,從而減少庫存和物流工作。
降低材料成本、機加工成本。相比一些傳統工藝加工的零部件相比,增材制造技術生產出的零部件加工余量小,加工周期短。
適合整體設計制造,提高結構效能和可靠性。如圖2所示將發動機轉子葉片與輪盤進行整體設計與制造,與傳統結構相比,由于省去了榫頭、榫槽和鎖緊裝置,可使發動機重量減輕20%~30%,零件數量減少50%,結構更加簡化,可靠性更高。同時,避免了榫頭的氣流損失,提高了壓氣機工作效率。
但同時,增材制造技術也有一定的局限性,主要表現在以下幾個方面:
工藝制造。增材制造不適于直接制造高精度零件。由于通過增材制造技術制造的零件是一層一層堆積而成,所以每一層都有它的厚度,這就決定了它的表面粗糙度難以企及傳統的減材制造方法。同時,由于存在一些難以克服的問題,它很難制造類似軸承、滾珠類的產品。
材料領域。增材制造技術還未形成廣泛的工業應用,最主要原因是適用原材料種類有限,許多原材料不能滿足設計要求。原材料是用于逐層堆積制作零部件的基礎原材料,也是增材制造技術的核心。目前可應用于增材制造的原材料種類較少,大量材料的應用潛能也未開發出來。
適航取證。目前各大航空發動機公司對增材制造的實際應用顯得異常審慎。如霍尼韋爾航空航天集團通過增材制造技術生產的零部件仍然只是用于適航取證的測試件,并未投入實際生產中。事實上,在航空制造領域,短時間內增材制造技術還無法完全替代傳統的制造工藝。一些企業希望從風險最低的、小的零部件開始,逐步推進,并以最安全的方式進入到生產階段。對于新技術的應用,提倡循序漸進的開發和使用,無論是原材料、工藝還是系統方面,都要經過嚴格的驗證,在被確認是成熟的且具有長期利用價值后才會取得適航許可,從而確保萬無一失。
總之,金屬增材制造技術作為一種兼顧精確成形和高性能成形需求的一體化制造技術,已經在航空制造領域顯示了廣闊和重要的應用前景。但是,相比于傳統鑄鍛等熱加工技術和機械加工等冷加工技術,金屬增材制造技術的發展歷史畢竟僅有近30年,其技術成熟度相比傳統技術還有很大差距,在很大程度上制約了金屬增材制造技術在航空領域的應用。這也意味著,對于金屬增材制造技術,仍有大量的基礎和應用研究工作有待開展。
來源:中國航空報