前幾年,我們看到發達國家的汽車模具行業似乎在萎縮。因為,當時認為模具生產離不開人的手工勞動,發達國家具有工資成本高、沒有人愿意干這一行等因素,模具行業大有向第三世界轉移的趨勢。
通過豐田的發展,我們有了一些新的認識。
模具生產越來越依賴高科技,完全可以把人工勞動降到很低,汽車對模具生產的需求最重要的是高質量和短周期,在大規模汽車生產中,模具本身的成本遠遠不如模具的使用成本更重要。從這一點上看,目前我們的模具生產不具什么優勢,這種工業轉移也不會成潮流,這十多年來,我們通過硬件的技術引進得到的技術進步,并沒有彌補上因人家更加努力地追求技術進步而帶來的新的差距。換個角度說,如果汽車模具行業真的向第三世界轉移的話,那一定是個夕陽產業,目前,汽車模具在車身材料沒有突破性變化的情況下,還是有一定的發展空間和需求的。
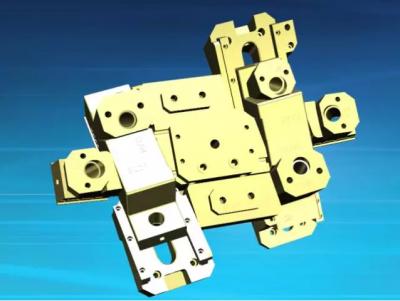
一.重點發展計算機技術
豐田模具制造技術發展的重點,在于突出計算機的應用,越來越多的人從生產現場轉移到計算機前。實體設計加上數控編程,取代了人工實型制作和機床操作。精細模面設計和精細數控編程大大減少了鉗修,高精度加工取消了模具的研合、修配。現在數控編程人員已超過了現場操作工人,數控編程的工時費用,超過了機床的加工工時費50%,編程的周期超過了機加工周期。
計算機技術應用的發展,目前沒有降低模具成本,但模具生產已從依賴人的技巧轉向數控化的自動、半自動化生產,這種高精度和無人化加工,使模具和產品件的質量有了極大的提高,生產周期大大縮短,計算機技術使模具制造技術又達到了一個新的高度。
相比較就可以看出,國內目前的計算機應用還比較初級,并不是我們的機床和軟件不行,而是在應用的基礎技術上有很大的差距,即使是把豐田的技術全搬來,真正做到那種效果,也不是一件容易的事。
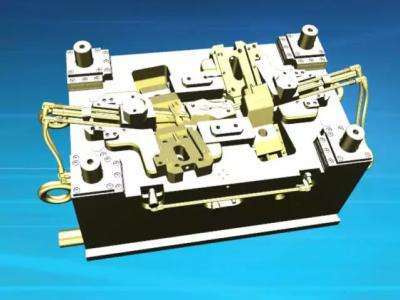
二.消滅鉗工
原來我們認為,模具這種單件生產、型面復雜的產品,離開手工是不可能的,而豐田提出要消滅鉗工。消滅鉗工是一種目標,主要是指極大減少或完全避免修磨和調整鉗工(裝配鉗工還是要的)。正如我們在前面所介紹的,目前豐田的這一目標已基本實現,除修磨拉延面和拉延凸圓角外,推磨、修模和調配鉗修,已大部分屬于異常或彌補設計、制造的缺陷,不再是一件必要的和正常的工作。
舉個例子,拉延模型面的光潔度歷來是我們強調的質量標準,過去為達到這一點主要是靠鉗工推磨。為減少或不推磨,就要減少銑削刀痕余量,有人主張采用垂直型面加工的五軸銑床,也有采用數控型面磨。這些豐田也都采用過,但實踐證明,五軸機床成本高、效率低,編程十分困難,效果也十分不理想。最后,豐田采用高速、小移行的三軸銑削加工方式,得到高精度型面,把圓角人工推磨,而其他型面干脆不修磨,模面帶刀痕拉延。結果證明,雖然模面談不上光潔度(還帶刀痕呢),但即使是表面質量要求很高的轎車外板件,除制件內表面有一些拉痕外,對有用的制件外表面沒有任何不良影響,就是需要電鍍的那些模面,也同樣是帶刀痕電鍍。據說德國和美國有些汽車模具廠也早已廢除了型面推磨。這對那些追求模具表面光潔度的人來說,真是命運開了一個大玩笑。同樣,對型面凹角采用清虧,立面加工采用30度頭防讓刀,用不等間隙控制制件成型壓力等等各種方法,現在凸凹模的配合精度,使研合和鉗修失去意義。
因此,某種意義上的消滅鉗工,不再是一個夢。當然,在國內,目前一個模具廠怎樣說服用戶接受這種帶刀痕的模具還是一個大課題。
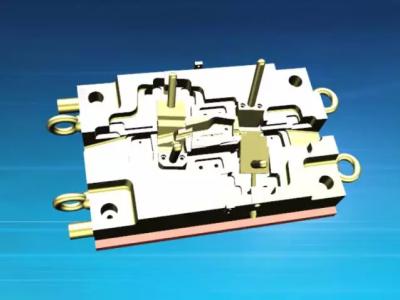
三.一體化加工
豐田的機加工車間現場,有三種數控加工線:
第一種是由幾臺床身可互換的數控機床組成的加工線,一條線里包括底面加工、臥銑、粗銑、精銑各種機床,配套分工明確,工件換機床時不必重新裝卡找正,這條流水線大約是80年代的產品。
第二種是帶立體倉庫的無人職守的柔性加工機群,這是90年代初的產物。
第三種是近年才投入使用的粗精加工一體化、高速、高精度、五面加工中心。
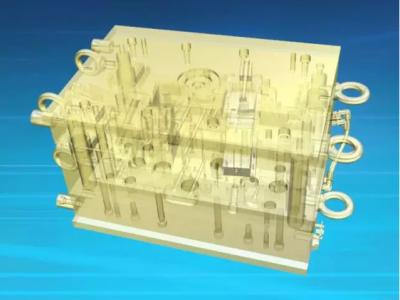
第一種加工線,它的單機就是我們目前使用的數控機床,但機床為多工作臺式,它的不重新裝卡找正方面效率很高。而我們還基本上停留在單機作業的水平上,很值得我們借鑒。對于柔性加工機群,雖然很先進,但操作起來很困難,準備工作和時間很長,如果沒有很大量的精加工任務,使用起來并不實用,就是在豐田也是如此,看來這不是一個成功的方向。
一體化加工中心是目前正在發展的最新技術,它的優點是,集各種機床優點之大成,除底面加工之外,一次裝卡,粗、精、臥、高功率、高精度、高速面面俱到,十八班武藝樣樣精通,加工效率很高。缺點是機床成本很高,需要環境要求也很高,用它來粗活、重活一起干時是不是很經濟呢?還不得而知。但,無疑這是一個很理想主義的技術,代表著數控加工技術的發展,應引起我們的注意。
文章來源:模具人雜志